What is Porosity in Welding: Comprehending Its Causes and Enhancing Your Abilities
Porosity in Welding: Identifying Common Issues and Implementing Best Practices for Avoidance
Porosity in welding is a prevalent issue that commonly goes unnoticed until it creates significant troubles with the integrity of welds. This common issue can endanger the strength and resilience of welded frameworks, positioning security dangers and resulting in costly rework. By comprehending the source of porosity and applying efficient prevention strategies, welders can significantly boost the high quality and dependability of their welds. In this discussion, we will certainly explore the vital factors adding to porosity development, analyze its destructive impacts on weld performance, and talk about the best techniques that can be taken on to reduce porosity event in welding processes.
Common Reasons For Porosity
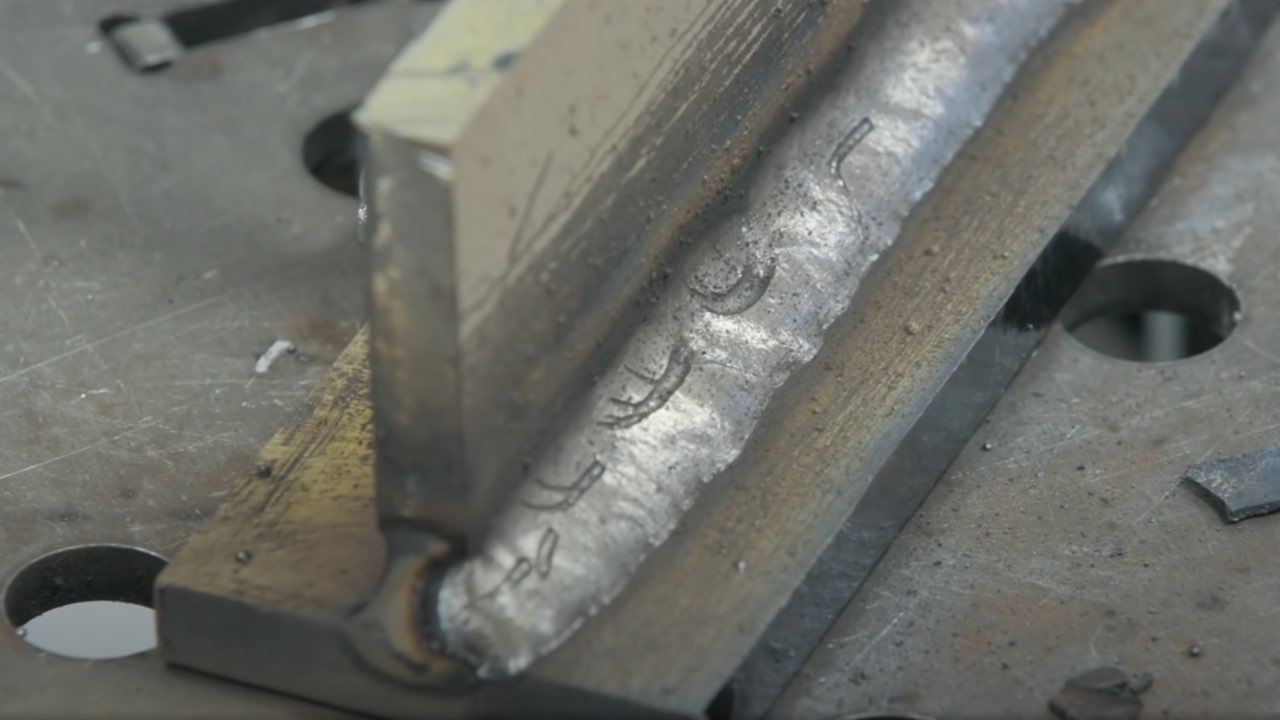
An additional regular wrongdoer behind porosity is the existence of contaminants externally of the base metal, such as oil, grease, or rust. When these pollutants are not effectively removed before welding, they can vaporize and come to be caught in the weld, causing flaws. Utilizing unclean or damp filler products can present pollutants right into the weld, adding to porosity issues. To reduce these typical reasons for porosity, complete cleansing of base steels, appropriate shielding gas option, and adherence to optimal welding criteria are necessary practices in achieving premium, porosity-free welds.
Influence of Porosity on Weld High Quality

The existence of porosity in welding can dramatically jeopardize the architectural stability and mechanical buildings of welded joints. Porosity creates spaces within the weld metal, compromising its general strength and load-bearing ability.
Welds with high porosity degrees often tend to exhibit lower influence strength and minimized capacity to warp plastically before fracturing. Porosity can hamper the weld's capacity to successfully transmit pressures, leading to early weld failing and prospective safety risks in crucial frameworks.
Best Practices for Porosity Prevention
To boost the architectural stability and quality of welded joints, what specific steps can be applied to reduce the incident of porosity during the welding process? Making use of the appropriate welding strategy for the specific product being bonded, such as readjusting the welding angle and gun setting, can better stop porosity. Normal assessment of welds and instant remediation of any concerns identified throughout the welding process are vital methods to prevent porosity and generate high-quality welds.
Importance of Correct Welding Strategies
Applying appropriate welding techniques is vital in ensuring the architectural honesty and high quality of bonded joints, building on the structure of efficient porosity prevention actions. visit Welding techniques directly affect the overall strength and durability of the bonded framework. One vital aspect of correct welding strategies is preserving the correct heat input. Extreme warm can result in boosted porosity because of the entrapment of gases in the weld swimming pool. Alternatively, inadequate warmth might lead to insufficient fusion, developing potential powerlessness in the joint. Furthermore, making use of the suitable welding specifications, such as voltage, existing, and travel speed, is important for achieving sound welds with very little porosity.
Moreover, the choice of welding procedure, whether it be MIG, TIG, or stick welding, ought to align with the particular needs of the job to guarantee optimal results. Proper cleaning and preparation of the base metal, along with choosing the appropriate filler product, are also vital parts of skillful welding strategies. By sticking to these best methods, welders can minimize the risk of porosity development and generate top notch, structurally sound welds.

Checking and Top Quality Control Actions
Quality assurance measures play a crucial role in verifying the honesty and dependability of bonded joints. Evaluating procedures are important to discover and avoid porosity in welding, guaranteeing the Full Article strength and toughness of the last product. Non-destructive testing techniques such as ultrasonic testing, radiographic testing, and visual evaluation are typically used to recognize possible issues like porosity. These techniques permit for the analysis of weld top quality without compromising the integrity of the joint. What is Porosity.
Conducting pre-weld and post-weld inspections is likewise important in preserving quality assurance standards. Pre-weld assessments involve validating the products, tools setups, and cleanliness of the workspace to prevent contamination. Post-weld evaluations, on the other hand, examine the last weld for any flaws, consisting of porosity, and verify that it go to my blog meets specified requirements. Implementing a comprehensive quality control plan that consists of detailed screening treatments and inspections is critical to lowering porosity issues and ensuring the total quality of welded joints.
Final Thought
Finally, porosity in welding can be a common issue that affects the top quality of welds. By identifying the common reasons for porosity and implementing finest practices for avoidance, such as appropriate welding techniques and testing procedures, welders can ensure top quality and trustworthy welds. It is vital to prioritize prevention techniques to decrease the incident of porosity and keep the integrity of welded structures.